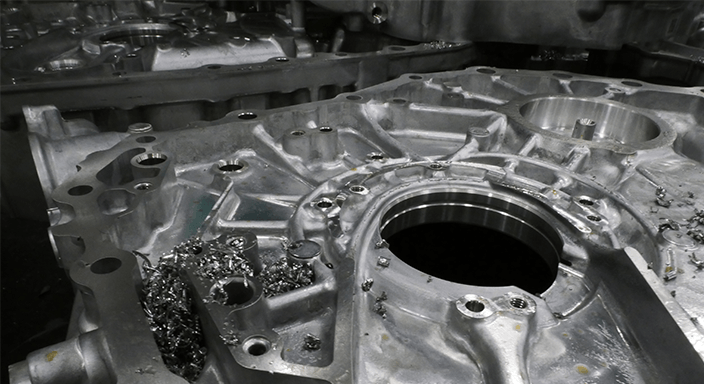
Aluminum Transmission Casting Parts Washer
Removal of machining debris for a North American Automotive Manufacturer
A North American automotive manufacturer reached out to us to create a cleaning system for freshly machined aluminum castings at a higher rate of parts/minute. Each part had a complicated geometrical casting that produced many holes and cavities where cleaning solution would build up and not get thoroughly cleaned through the wash, rinse, and blow-off processes. With the complexity of the washer, we also had to make sure that no parts got scratched when going through the 4 stages of the washer.
The process is new to the company’s plant, but similar to a previous one. The process is to go from the machining plant that will wash off the excess chips and coolant off the part, then leak test them. From there, they will be shipped to an assembly plant to be put together.
The Challenge:
Each stage presented a different challenge.
- Clean, rinse, and dry parts in a 16’ long floor space
- Protect the bottom surface of the parts from getting scratched
- Keep everything at an ambient temperature to allow parts to be leak tested upon exiting the washer
- Efficiently and effectively remove cutting oil and chips from aluminum castings at a rate of one part every 41 seconds
During the second stage of the wash cycle, cutting oil and chips needed to be fully removed from the part. Additionally, parts needed to be dried upon the exit of the washer and maintain the required temperature.
The Solution:
With the challenges Arnold Machine was presented, our team created unique solutions.
- Creation of a 4-stage 30” Belt Cleaning System
- Use of a polypropylene (plastic) belt throughout the machine to prevent scratching
- Utilizing a 140 GPM at 45 psi pump using several clip-on adjustable polypropylene spray nozzles for the first wash and rinse stage
- Designed rotary stainless-steel nozzles powered by a 36 GPM at 300psi pump to wash all sides of the part to allow for sufficient chip and cutting fluid removal
- Creation of a unique blow-off system using air knives and high-volume pressurized air cannons
All the pumps used in the cleaning system were fed through a stainless-steel bag filter housing and ran through a single Boll automatic back flushing filter. Each pump pulled from a 350-gallon wash solution tank. Our blow-off system allowed us to target areas of the parts where the cleaning solution was collecting which was making it difficult to remove. At run-off, we met the customers 3 major requirements they were looking for (removal of aluminum machining chips, part dryness, and exit temperature of the transmission case).
The Results:
Despite the many cavities and holes in the casting, the machining debris was completely removed from the part. No scratches were present on the castings and the ambient air temperature allowed for leak testing. The machine was able to efficiently run 1 part every 41 seconds.
The end results were above and beyond our customers’ expectations and they were happy with not only the cleaning/chip removal, but how well the parts were dried as they exited the system.