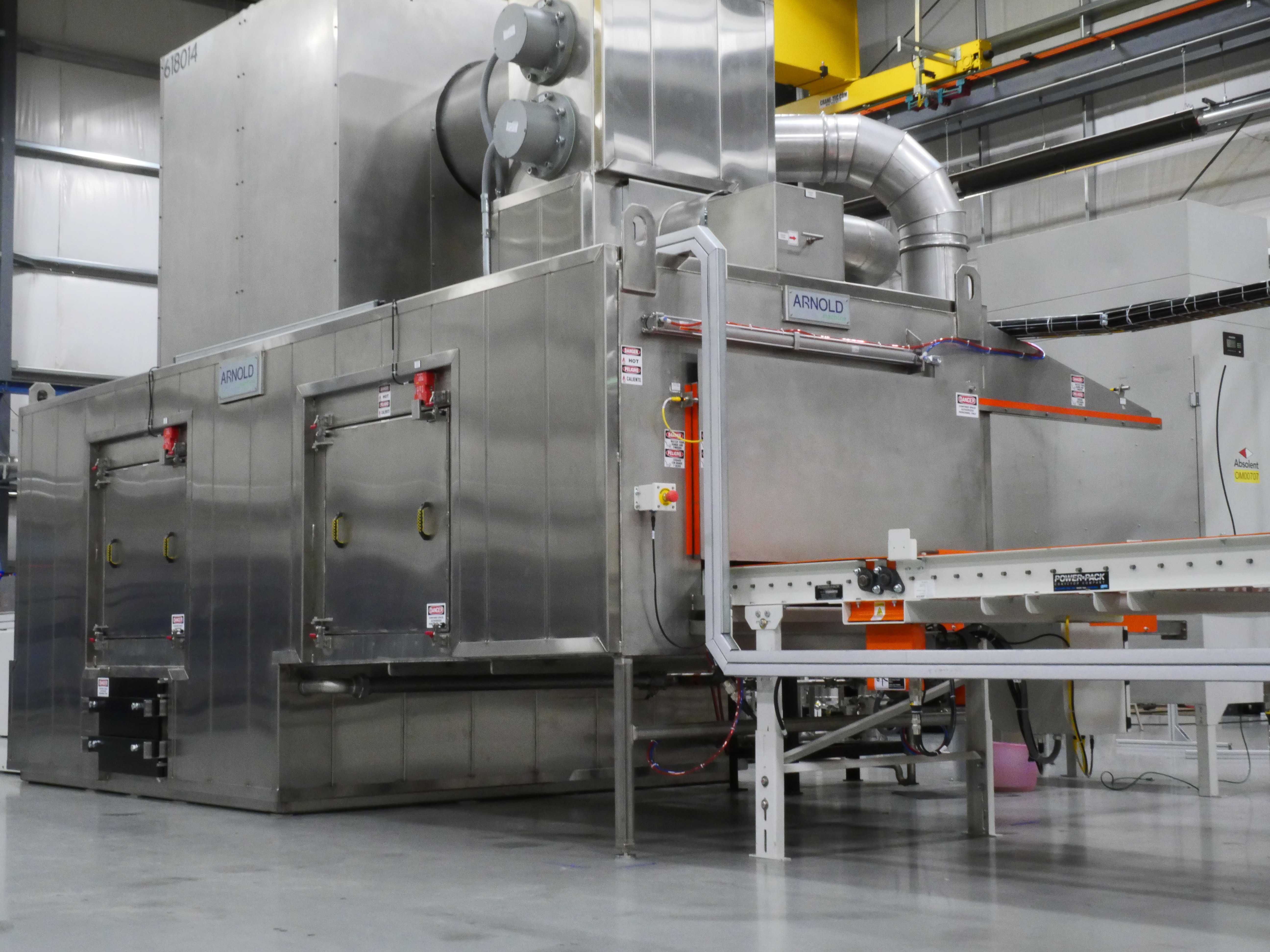
Benefits of a Parts Washer vs. Manual Cleaning Methods
Properly washing your industrial parts can improve employee safety, reduce labor requirements, and increase efficiency. While manual cleaning methods may seem cost-effective and convenient, they often fall short in terms of effectiveness and time efficiency.
There are many different methods of cleaning parts, each with its own advantages. Read on to learn more about industrial parts washing machines versus manual cleaning methods and which is right for your application.
Parts Washer Benefits
An industrial parts washer will allow you to clean your parts with the least amount of time and labor spent performing the task. Simply put your dirty parts into the machine, press a few buttons, and wait for the process to finish.
Many parts washers, such as those from Arnold Machine, allow you to use aqueous-based cleaning solutions that are less toxic to employees and better for the environment. Chemical solvents can release volatile organic compounds (VOCs) into the air and require expensive wastewater treatment.
Parts washers require fewer people to clean parts. Depending on the volume of the parts you need to wash, it generally only requires one person to tend to a parts washer that can clean volumes more than manually cleaning can. These operators can be working elsewhere within the facility instead of cleaning parts.
The Different Ways of Cleaning Parts
There are many different ways of washing industrial parts, including:
Manually—Washing parts manually often involves a worker standing over a sink and using a wire brush to scrub the parts clean. Harsh chemical solvents can get on the skin and clothing of the worker while toxic fumes waft into the air. It can take an hour or more to clean a single part properly.
Pass-through washers—Also known as “conveyor washers,” this category of parts washers includes:
- Belt washers
- Parallel chain washers
- Powered roller conveyor washers
- Monorail washers
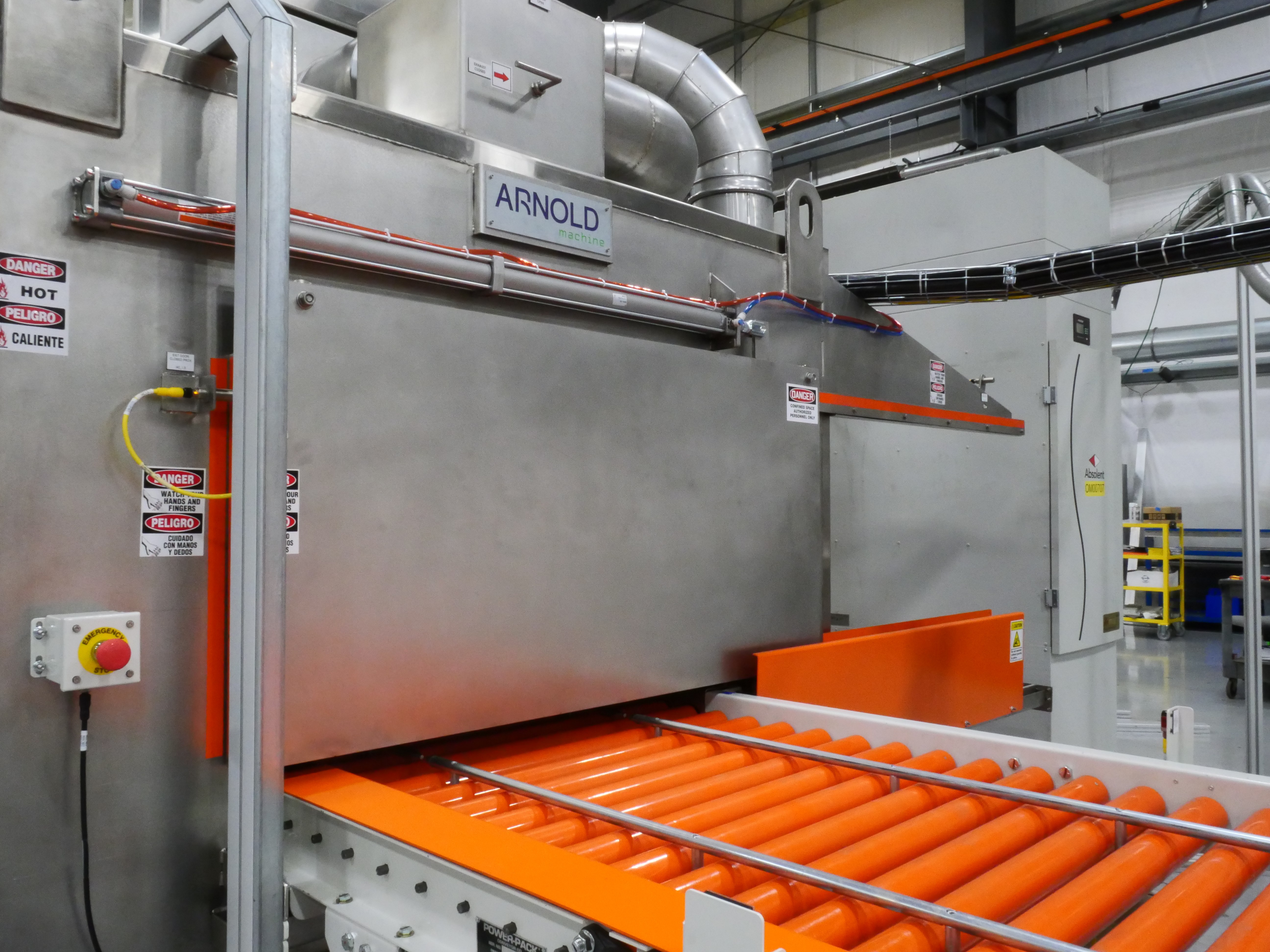
Workers will put dirty parts on a conveyor-like system that sends them through the washing and drying process. Conveyor washers are ideal for high-volume, in-line cleaning applications.
Rotary Table washers—You can have a rotary washer configured to clean a wide range of parts. Standard rotating table sizes range from 24 to 72 inches in diameter, which can clean parts with heights of up to 120 inches. Custom sizes are available.
Rotary Basket washers—These parts washers are ideal for precision, batch, and ultrasonic cleaning. Standard rotary basket washers come in 2, 4, 6, and 8-basket capabilities. Arnold Machine can also configure them for partial immersion, spray, and full immersion. Ultrasonic is also an available option.
Ultrasonic washers—An ultrasonic industrial parts washer uses high-frequency sound waves that create microscopic bubbles in a cleaning solution. These bubbles implode and release high-energy shock waves that remove dirt, grease, and grime from parts.
Ultrasonic parts washers can remove contaminants from parts that may be difficult or impossible to clean manually. The high-energy shock waves generated by the collapsing bubbles can penetrate even the tiniest crevices and remove stubborn contaminants.
Immersion washers—These parts washers immerse very small to very large parts in a tank filled with a solution. There is a wide range of available options and setups to meet almost any industrial parts cleaning need.
Arnold Machine Competitive Advantages
When selecting the right automated industrial parts washer, pay close attention to the manufacturer. Arnold Machine builds our parts washers with high-quality components designed to operate in extremely harsh and dirty conditions.
We have a unique ability to incorporate robotics and other automation features into the parts washer process. Companies can reduce labor dependency and increase quality control by automating parts washing tasks.
For example, a major firearms manufacturer decided to bring parts washing in-house for better quality control and to overcome potential product shortages. Arnold Machine designed and built a custom unit that combined automation and parts washing. The firearms manufacturer can now run full production volume with only one worker running the machine.
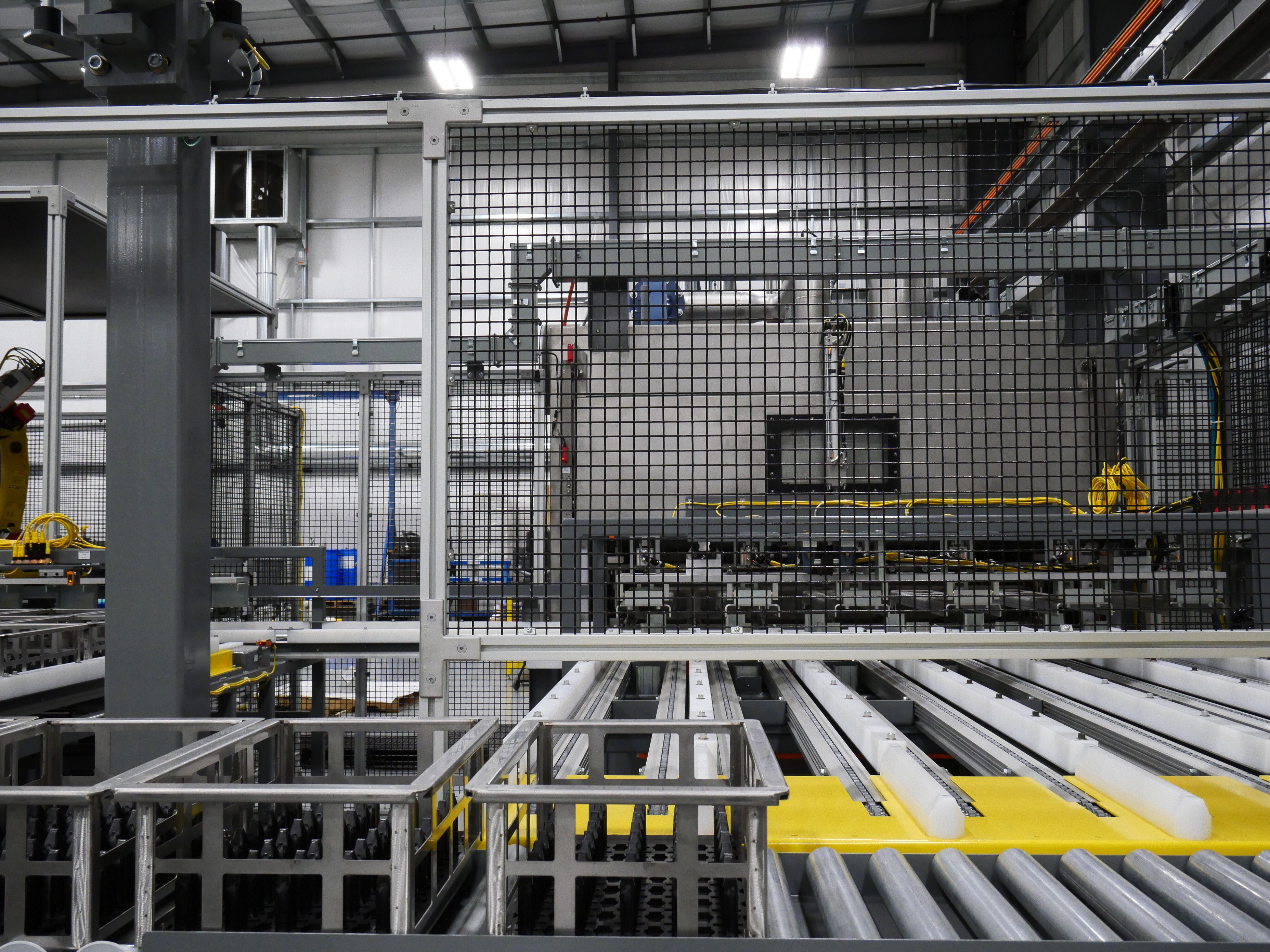
What sets Arnold Machine apart from other parts washer manufacturers is that we work very closely with our clients to design customized solutions to meet their needs. Other benefits of working with Arnold Machine include:
- The customer will be able to participate in design reviews to ensure that the end product will be exactly what they envisioned before they sign off on a finished design, allowing us to proceed to the fabrication stage.
- Our top-notch customer service team will ensure you’re 100% comfortable with the end product and will take care of all your service needs in the future.
- Our team collaborates with our customers at all stages of the process to keep them involved—sales, design, build, runoff, install, and after start-up.
- We design our washers with the end user in mind. We want your team comfortable accessing, using, and maintaining this piece of equipment.
- Our parts washers are designed and manufactured in the USA - our factory is in Tiffin, Ohio.
Which Parts Washer Is Right for Your Application?
Arnold Machine specializes in designing and building customized parts washers for almost any application imaginable. Our expert engineers will work closely with you to help solve your toughest parts-washing challenges. Click below to learn more.