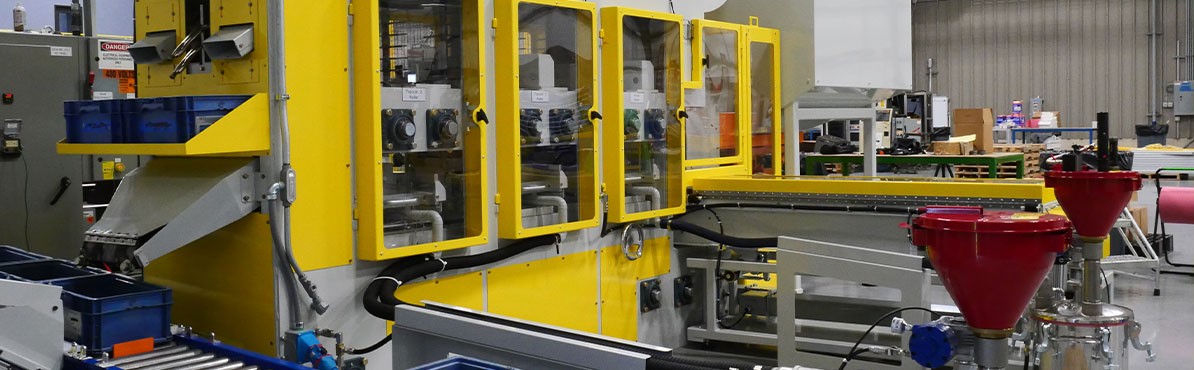
Choosing the Right Paint Conveyor System: Factors to Consider
Applying coatings is a vital step for manufacturers in many different industries. However, paint systems are often messy, inconsistent, dangerous, and labor-intensive. This leads to various issues that ultimately undermine performance and profitability.
An automated spray system will transform your operations by improving quality, efficiency, and safety. Read on to learn how to choose how to choose a paint conveyor system.
KEY PAINT CONVEYOR CONSIDERATIONS
There are several key factors you need to consider when choosing the right paint conveyor system:
Efficiency and Productivity
Companies invest in paint conveyor systems primarily to improve efficiency in the spraying process. The conveyor systems allow continuous or semi-continuous painting. This reduces manual handling and downtime between paint applications. It increases throughput, production rates, and efficiency.
The operators need to load each part the same way every cycle. They must maintain a consistent temperature. The spray guns must dispense the correct amount of paint at the right speed every time. Doing these steps consistently provides uniform quality and improved production rates.
Our Chain-on-Edge conveyors transport parts nonstop across different zones. The continuous movement increases the overall pace of production. It also allows accurately indexing each part when required. Indexing optimizes cycle times for better efficiency, as demonstrated in this case study.
Consistent and High-Quality Paint Application
Conveyor systems enable consistent and precise paint application. This helps to ensure uniform coverage, thickness, and finish. Automated or controlled movement along the conveyor helps eliminate variations caused by human error. The result is a superior paint quality and a professional appearance for the finished products.
Our Chain-on-Edge spray systems present the part at the same temperature. This allows the coating application to achieve a consistent dry film thickness without adjusting the spray gun settings. We also validate this via part temperature sensors and flow rate measurement.
The heaters our machines use maintain consistent part preheating and drying temperatures. This reduces the fluid and air adjustments needed to achieve a uniform dry film thickness on dissimilar parts.
Reducing Paint Waste and Costs
Overspray and incorrect paint usage during manual application lead to excessive waste. Paint conveyors optimize material utilization through accurate dispensing and transfer efficiency. This leads to cost savings in paint materials, increased process efficiency, and a more sustainable approach to painting operations.
Repeatable and documentable spray gun positioning comes standard on our Chain-on-Edge machines. We also offer programmable spray gun positioning options that maximize transfer efficiency by optimizing the spray gun angle and position in relation to the target. They also control the speed of the spray gun motion.
The fluid flow monitoring feature allows for a reduction in wasted material costs. It also validates the amount of material the system utilizes to achieve a consistent dry film thickness.
Health and Safety
Painting processes often involve hazardous materials and fumes. Paint conveyor systems can incorporate safety features such as enclosed booths, ventilation systems, and proper exhaust systems to ensure the health and safety of workers.
These systems contribute to a safer workplace by minimizing exposure to harmful substances and creating controlled painting environments. We maintain 100% VOC capture inside the spray booth and do not recirculate any volatiles across the oven heat source.
Meeting Quality Standards and Regulations
Industries such as automotive, aerospace, and manufacturing have strict quality standards and regulations for paint application. Paint conveyor systems provide a controlled and standardized process that helps meet these quality requirements. This helps to ensure compliance with industry-specific standards and regulations.
Arnold Machine spray systems can document all process parameters to help provide repeatable:
- Process quality
- Spray gun positions
- Air and fluid settings
- Part temperatures
- Rotation speed
- Spray gun positioning
- Conveyor speed
- And more
The programmable controls enable you to optimize your spray parameters once. You can then repeat it as many times as you like via a part recipe.
Flexibility and Customization
Paint conveyor systems offer flexibility and customization options for different part sizes, shapes, and production requirements. Adjustable conveyor speeds, variable spray patterns, and customizable paint booths or drying systems allow for versatility in handling a wide range of products.
Arnold Machine spray booth robots maximize the universality of the spray process for a high range of complex geometries or low-volume product mixes. The adaptability of simple fixtures provides cost savings by avoiding the need for intricate configurations. This simplifies features while maintaining versatility.
Utilizing robots for automatic spray gun positioning provides the most flexible solution for current and future spray applications. However, we can remove this option if your product mix does not require it.
Seamless Workflow Integration
We can integrate paint conveyor systems into existing production lines or painting processes to create a streamlined workflow while minimizing disruptions. Integration with automation, robotics, or other equipment enables smooth material handling, data exchange, and process synchronization. This connectivity creates an efficient and coordinated manufacturing process.
Arnold Machine offers several options to keep pace with your upstream and downstream production requirements. There are also additional options for automated material handling to and from these operations.
Benefits of MaaS and Chain-on-Edge Spray Machines
In addition to the ability to purchase a Chain-on-Edge system outright, we also offer a Machine-as-a-Service (MaaS) program. It allows manufacturers to get our state-of-the-art spray equipment on their floors without a massive capital investment.
MaaS unlocks substantial advantages for chain-on-edge spray machines. You pay based on usage and can scale capacity as needed. There are no complex ROI calculations or acquisition hassles.
Arnold Machine builds and delivers the customized machine to your facility. Your only upfront cost is the installation and a commission fee that includes employee training and spare parts. You pay a pre-negotiated rate for each minute the machine is available and active.
You pay less when the machine isn’t in use. You pay nothing if the machine is down for scheduled maintenance or Arnold Machine responsible downtime. We also handle the upkeep so you can focus on manufacturing.
MaaS is not a lease. Instead, it’s a partnership based on performance where the cost is truly an operating expense. We hold the title to the machine, and there are no contracts—our machine stays on your floor as long as you need it. If things aren’t working out as expected, simply return it.
OPTIMIZE YOUR WORKFLOW WITH CHAIN-ON-EDGE PAINT CONVEYOR SYSTEMS
Transitioning to automated chain-on-edge conveyor painting streamlines workflows through improved quality, efficiency, and safety. Machine-as-a-Service allows any sized manufacturer to gain a competitive edge without a massive initial cash outlay.
Click below to discover how our innovative painting automation systems can transform your manufacturing workflows.